Projects
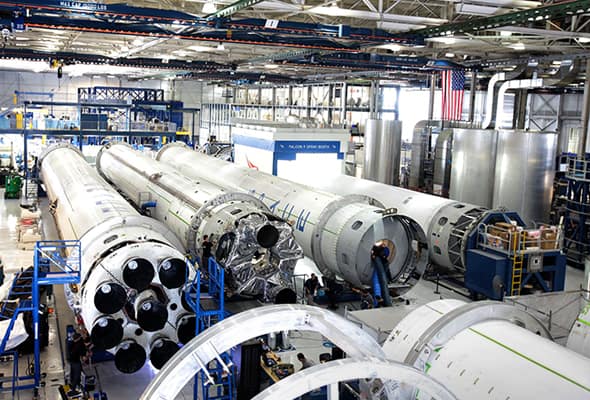
Mercury Oxidation Performance of SCR Catalysts
This project examined the performance of five SCR catalysts for their mercury oxidation performance under a range of operating conditions. The parametric testing included variations in chlorine, bromine, temperature, flow rate, and NH3/NOx ratio (i.e. deNOx). Plate, honeycomb, and corrugated catalysts were all tested, along with one formulation of advanced catalyst that was optimized to promote mercury oxidation.
The testing was conducted at the Mercury Research Center as part of a joint study by EPRI and Southern Company. The results have helped guide utilities in determining the expected mercury oxidation rates for various flue gas conditions. The testing has also provided guidance for the implementation of mercury oxidation enhancement processes, such as bromine or chlorine injection, fuel switching, and catalyst management.
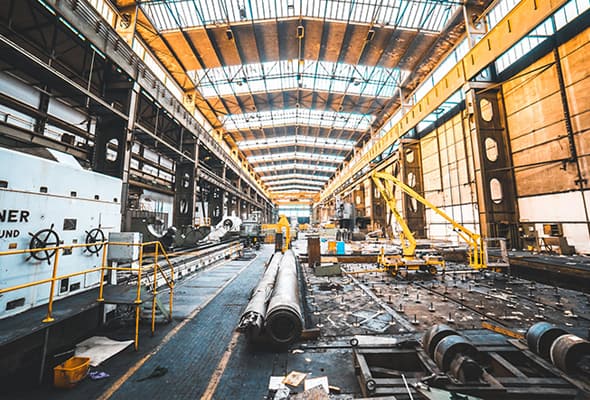
Long-Term Comparative Performance of New and Regenerated SCR Catalysts
The long-term performance of new and regenerated catalysts was investigated in a multi-year project which utilized data from full-scale commercial SCRs. The purpose of the project was to determine if regenerated catalyst deactivated or lost physical strength in a way that was consistent with new catalysts, or if the regenerated catalysts exhibited accelerated deactivation or strength loss. This information is important to long-term economic and technical evaluations where the use of new and regenerated catalyst is compared. Numerous utility sites were included in the study, covering a range of catalyst manufacturers, fuels, and boiler designs.
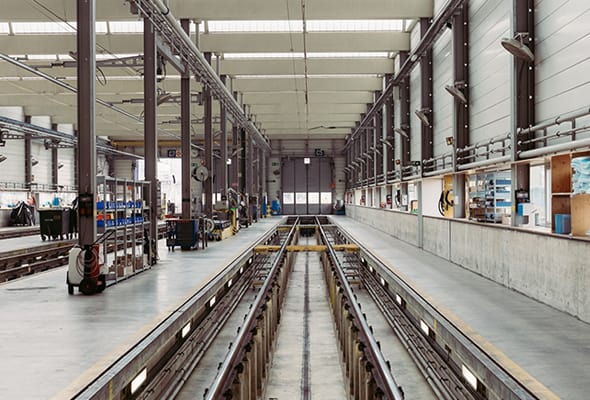
Protocols for Laboratory Testing of SCR Catalysts
Protocols were developed for EPRI for the testing of SCR catalysts in laboratory test reactors for deNOx and SO2 conversion, and mercury oxidation. The protocols provide guidance related to the appropriate test apparatus design, test procedures, measurement procedures, data reduction, and data reporting. The protocols are designed to aid in the interpretation of data, ensure the comparability of data between different laboratories, and aid in the selection of test conditions.
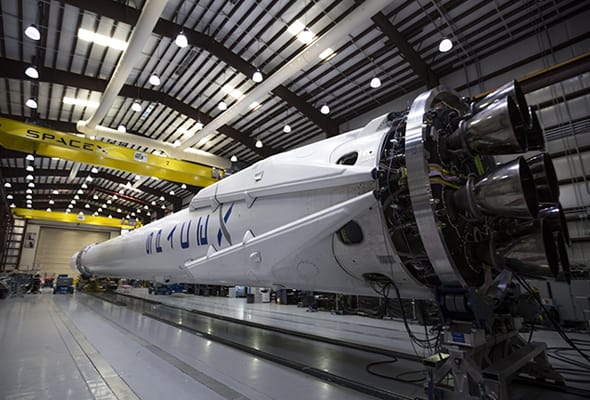
Fly Ash Ammonia Removal Processes
This multi-year project examined a number of processes for the removal of ammonia from fly ash. Chemical, thermal, and hybrid processes were evaluated in terms of both technical and economic performance. The information helps guide utilities in the selection of ammonia removal processes, and helps provide valuable technical information to aid in the understanding of the underlying chemical and physical processes which affect fly ash ammonia behavior during handling, storage, transport, and treatment.
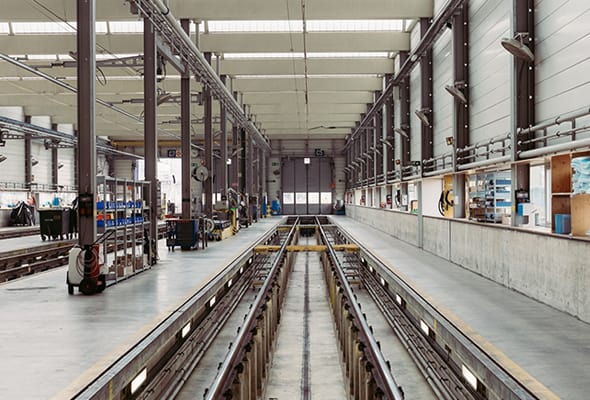
Catalyst Management for Mercury Control
This project developed catalyst management strategies to help improve mercury oxidation for coal-fired facilities equipped with SCRs. Data from a wide variety of sources was utilized to develop the strategies, which vary in terms of the level of mercury oxidation that is required, SCR and boiler design, and fuels utilized. The strategies can be used alone or in combination with mercury oxidation enhancement processes, such as bromine injection, and are applicable to mercury capture in a number of devices including the ESP, wet scrubber, dry scrubber, and sorbent injection/capture systems.
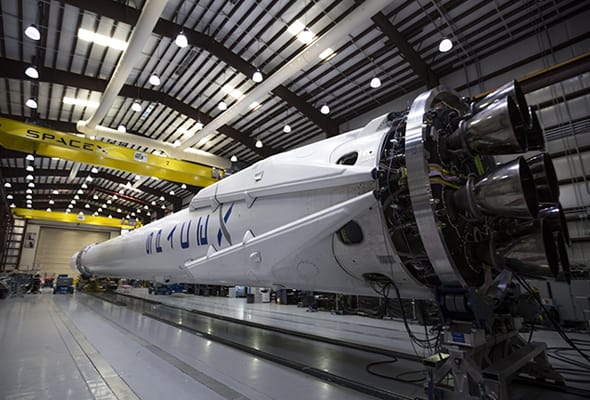
Site Mercury Evaluations
Several site mercury evaluations have been performed, which provide an integrated assessment of mercury behavior around a particular operating unit or plant site. These evaluations examine the mercury behavior beginning with the fuels being fired and ending at the stack, thus covering the entire flue gas train. The evaluations are designed to help improve mercury emissions by operating the entire unit in an integrated fashion which maximizes mercury oxidation and capture. Various effects are considered, such as fuel composition, SCR and air preheater oxidation, and capture performance through various devices such as the ESP and wet scrubber. The analysis also helps to optimize dedicated mercury control systems such as activated carbon injection. The ultimate aim of the evaluation is to provide maximized consistent mercury removal at minimum cost to the utility, utilizing processes already in place, if possible, to meet mercury emissions regulations.